Desalters are a critical element in a corrosion control program at a refinery or oil terminal and typically see the highest salt concentrations of any vessel on the site. It only stands to reason that they themselves would be protected from this highly corrosive environment with a capable coating yet often times they are either left uncoated or only minimally protected with a solvented glass flake epoxy coating. Belzona coatings have been used by major oil and gas operators to provide desalters with long lasting corrosion protection and have demonstrated usable lives well in excess of ten years. Corrosion allowances alone can be effective but generally only if the assumed operating conditions do not change. As is often the case, conditions do change and corrosion rates can increase to intolerable levels. Glass flake vinyl esters can provide short term protection but they have some deep flaws which result in relatively short usable lives as compared to solvent free epoxy novolacs.
A global oil and gas asset owner selected Belzona® 1391S for several desalters at one of their oil terminals in 2008 and again in 2009 which operate at 230°F (110°C) and 30,000mg/L salt. This selection was driven by their internal testing which identified Belzona 1391S as the most capable coating and their operating experience which demonstrated that glass flake vinyl esters blister and fail after only six years.
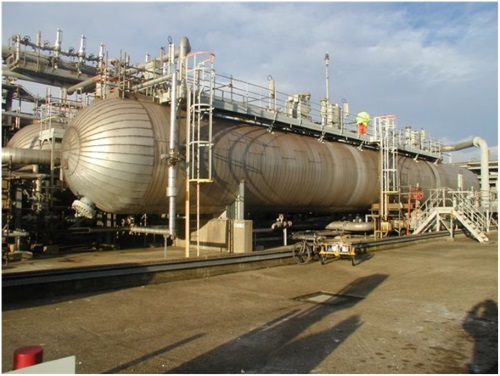 Figure 1: Desalters at an oil terminal which were lined with Belzona® 1391S in 2008 and 2009
Another oil and gas company selected Belzona® 1591 (Ceramic XHT) to line a desalter in 2002. Because of pressure to return the vessel to service faster than originally planned, surface preparation and application standard were compromised yet the coating lasted nine years before it was removed and reinstalled properly. Extremely fluid low permeation rates and tenacious adhesion allow Belzona’s high temperature coatings to protect surfaces in situations where lesser coatings would simply blister or disbond.
.jpg)
Figure 2: Lower half of desalter at the seven year inspection of Belzona® 1591 (Ceramic XHT). Coating was deemed fit for another five years of service during this inspection.
Why entrust a critical path vessel to corrosion allowance or a solvented coating when a truly durable solution which can tolerate fluctuations in feed stock composition and conditions can be installed for a fraction more?
Chris Lucas clucas@rumfordgroup.com 937-435-4650 RumfordGroup.com
|